Home / News / Industry News / What is the role of regular maintenance of fresh-air-system-motors?
Oct 07,2023
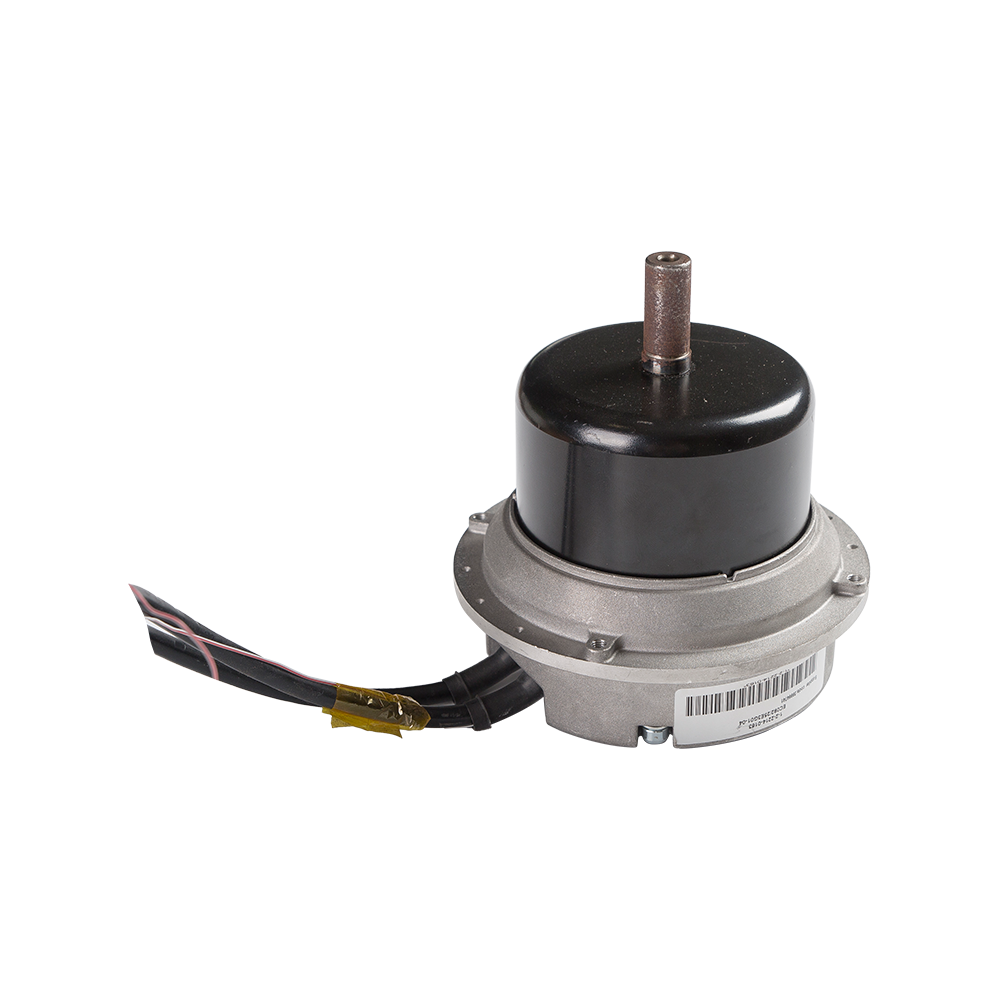
Home / News / Industry News / What is the role of regular maintenance of fresh-air-system-motors?
Oct 07,2023
surveillance and photography DC brushless motors interface with control systems in surveillance and photography equipment through a combination of electronic components, sensors, and control algorithms. The interface is designed to provide precise control over the motor's speed, position, and other parameters. Here's a general overview of how DC brushless motors are typically integrated into control systems: Electronic Speed Controller (ESC): DC brushless motors are commonly paired with Electronic Speed Controllers (ESCs). The ESC is a crucial component that regulates the motor's speed and direction. It interprets signals from the control system and adjusts the voltage and current supplied to the motor accordingly. Position Sensors: DC brushless motors often incorporate position sensors such as Hall effect sensors or encoders. These sensors provide feedback to the control system about the rotor's position, allowing for precise control of the motor's rotation. This feedback is essential for closed-loop control systems. Control Signals: The control system sends signals to the ESC to specify the desired motor speed, direction, and other parameters. These signals are typically in the form of pulse-width modulation (PWM) signals, where the width of the pulse determines the motor's speed. Closed-Loop Control: In many surveillance and photography applications, closed-loop control is employed for enhanced accuracy. The control system continuously receives feedback from the position sensors and adjusts the motor's operation in real-time to maintain the desired position or speed. This closed-loop feedback loop ensures precise and stable motor performance. Microcontrollers and Processors: Microcontrollers or digital signal processors (DSPs) are often used in the control system to execute control algorithms. These algorithms process the feedback from position sensors and generate control signals to achieve the desired motor behavior. The use of digital control allows for sophisticated and adaptive control strategies. Communication Protocols: Communication protocols, such as PWM or other digital communication protocols (e.g., I2C, SPI), facilitate the exchange of information between the control system and the DC brushless motor. These protocols enable seamless integration and communication within the overall system architecture. Safety Features: Control systems may include safety features such as current limiting, overheat protection, or fault detection mechanisms. These features enhance the reliability and safety of the overall system, especially in critical applications. By combining these elements, the integration of DC brushless motors into control systems for surveillance and photography equipment allows for precise, responsive, and customizable motor control. The use of feedback mechanisms, advanced control algorithms, and digital communication ensures that the motors operate optimally in diverse and dynamic operational scenarios.
MoreSurveillance and photography DC brushless motors are known for their ability to reduce electromagnetic interference (EMI), which is a significant advantage in applications such as surveillance and photography where sensitive electronic components are involved. Here's how DC brushless motors contribute to minimizing EMI: Brushless Design: Unlike brushed motors, DC brushless motors operate without physical brushes. The absence of brushes eliminates the sparking and arcing that can occur in brushed motors, which are common sources of electromagnetic interference. This inherent design feature makes DC brushless motors intrinsically cleaner in terms of EMI. Smooth Commutation: DC brushless motors use electronic commutation through sensors and controllers to determine the rotor position. This electronic commutation results in smoother and more controlled transitions between motor phases, reducing the likelihood of abrupt changes that can generate EMI. Precise Control Electronics: DC brushless motors are often paired with advanced control electronics that provide precise and optimized control over the motor's operation. This level of control allows for smoother and more predictable motor behavior, minimizing unintended electrical noise emissions. Shielding and Filtering: Manufacturers often incorporate shielding and filtering mechanisms in the design of DC brushless motors to further reduce electromagnetic interference. These measures help contain and filter out any residual noise generated during motor operation. Compliance with EMI Standards: Many DC brushless motors are designed and manufactured with a focus on meeting electromagnetic compatibility (EMC) standards. Compliance with these standards ensures that the motors produce EMI within acceptable limits, making them suitable for use in electronic systems where interference must be minimized. Isolation Techniques: In certain cases, isolation techniques may be employed to physically separate the motor from sensitive electronic components. This helps prevent direct transmission of electromagnetic interference to nearby devices, contributing to a cleaner overall system environment. By combining these design features and considerations, DC brushless motors can effectively reduce electromagnetic interference in surveillance and photography applications. This is particularly important in camera systems and other electronic devices where the quality of signals and data integrity are critical for optimal performance.
MoreThe use of DC brushless motors in surveillance and photography motors applications offers several advantages over other motor types, contributing to improved performance and reliability. Here are some key advantages: High Efficiency: DC brushless motors are known for their high efficiency, which translates to less energy loss in the form of heat. This efficiency is crucial in surveillance and photography equipment, where power consumption needs to be optimized. Low Maintenance: Unlike brushed motors, DC brushless motors have no physical brushes that wear out over time. This results in lower maintenance requirements and longer operational lifespan, making them a more reliable choice for continuous use in surveillance devices. Reduced Electromagnetic Interference (EMI): DC brushless motors generate less electromagnetic interference compared to brushed motors. This is important in surveillance and photography equipment, where sensitive electronic components such as sensors and communication devices may be affected by EMI. Precise Speed and Position Control: DC brushless motors offer precise control over speed and position, making them suitable for applications where accurate movement is essential. This precision is valuable in camera systems, ensuring smooth and accurate tracking or adjustments. Compact Design: DC brushless motors are often more compact and lightweight than their brushed counterparts. This is advantageous in surveillance and photography equipment, where space and weight considerations are critical, especially in portable or compact devices. Longer Lifespan: The absence of brushes in DC brushless motors contributes to their longer lifespan. In surveillance and photography applications, where reliability is paramount, having a motor with an extended operational life reduces the likelihood of unexpected failures. Quiet Operation: DC brushless motors generally operate more quietly than brushed motors. This is advantageous in photography, where camera noise can be a concern, and in surveillance applications, where discreet operation is often desired. Improved Control Integration: DC brushless motors can be easily integrated with advanced control systems and electronics. This facilitates the implementation of features such as feedback control, closed-loop systems, and precise motion profiles, enhancing the overall performance of surveillance and photography devices. Higher Torque-to-Inertia Ratio: DC brushless motors often have a higher torque-to-inertia ratio, providing faster acceleration and deceleration. This is beneficial in applications where quick and responsive movements are required, such as in pan-tilt-zoom camera systems. The advantages of using DC brushless motors in surveillance and photography include increased efficiency, lower maintenance, reduced EMI, precise control, compact design, longer lifespan, quiet operation, improved control integration, and a favorable torque-to-inertia ratio.
MoreBrushless motors deliver power and torque through a process known as electronic commutation. Unlike traditional brushed motors, which use brushes and a commutator to switch the direction of current in the motor windings, electric power tool brushless motors achieve commutation electronically. This electronic commutation is facilitated by the control system, which includes sensors, a microcontroller, and electronic circuits. Here's an overview of how brushless motors deliver power and torque, along with their typical performance curve: Rotor Position Sensing: Brushless motors incorporate Hall Effect sensors or other position sensing devices strategically placed around the motor to detect the position of the rotor. These sensors provide feedback to the control system about the rotor's current position within the stator. Electronic Commutation: Based on the feedback from the sensors, the control system determines when to energize specific coils or phases of the motor windings. Instead of using brushes and a commutator to mechanically switch the current direction, the control system electronically commutates the motor by energizing the appropriate windings at precise moments in the rotor's rotation. Sequential Phases: The motor windings are organized into phases, and the control system activates these phases in a sequence that corresponds to the rotor's position. By sequentially energizing the phases, the control system effectively produces a rotating magnetic field that interacts with the permanent magnets on the rotor, causing it to turn. Torque Production: As the rotor turns in response to the changing magnetic field, torque is produced. The torque generated is proportional to the current flowing through the motor windings and the strength of the magnetic field. The brushless motor is capable of delivering torque throughout its operating range, making it suitable for a variety of applications. Performance Curve: The performance curve of a brushless motor illustrates its characteristics in terms of speed, torque, and power across a range of operating conditions. In a typical performance curve: Speed-Torque Relationship: The curve shows how the motor's speed varies with changes in the applied torque. Brushless motors often exhibit high torque at low speeds and may maintain a relatively constant torque as speed increases until reaching a maximum speed. Efficiency Curve: The curve depicts the motor's efficiency at different operating points. Brushless motors are known for their high efficiency, especially in comparison to brushed motors, and they often operate at peak efficiency over a broad range of loads. Variable Speed Control: The electronic control system allows for precise control over the speed of the brushless motor. By adjusting the timing and duration of the current pulses supplied to the motor windings, the control system can modulate the motor's speed. This variable speed control is a key advantage of brushless motors in power tools. High Torque at Low Speeds: Brushless motors excel at delivering high torque at low speeds, making them well-suited for applications that require substantial power during startup or at low operating speeds. Linear Response: The response of a brushless motor to changes in input voltage or load is often more linear compared to brushed motors. This linear response contributes to stable and predictable performance. Regenerative Braking (in some applications): Some brushless motors used in certain applications, such as electric vehicles, can act as generators during braking events, converting kinetic energy back into electrical energy. This regenerative braking capability enhances energy efficiency.
MoreElectric power tool brushless motors are controlled using electronic systems that manage the operation of the motor by precisely adjusting the power supply. The control system typically involves the use of sensors, microcontrollers, and electronic circuits to regulate the speed, torque, and direction of the motor. Here are the key elements of the control system for brushless motors in power tools: Hall Effect Sensors: Brushless motors commonly incorporate Hall Effect sensors to detect the position of the rotor. These sensors are placed strategically around the motor to sense the magnetic field changes as the rotor rotates. The information from the Hall Effect sensors is crucial for determining the rotor's position and controlling the motor's commutation. Rotor Position Feedback: The signals from the Hall Effect sensors provide feedback about the precise position of the rotor to the motor controller. This feedback is essential for determining when to energize specific motor windings to maintain smooth and efficient operation. Microcontroller or Digital Signal Processor (DSP): A microcontroller or digital signal processor is the brain of the motor control system. It receives input from the Hall Effect sensors and uses this information to calculate the optimal timing for energizing the motor windings. The microcontroller executes algorithms to control the motor's speed, torque, and direction. Commutation Timing: The control system determines the optimal timing for commutating (switching) the power supply to the motor windings. This precise timing is essential for maintaining a continuous and smooth rotation of the rotor. Pulse Width Modulation (PWM): The power supplied to the motor windings is often modulated using Pulse Width Modulation. PWM adjusts the width of the electrical pulses, controlling the effective voltage applied to the motor. This modulation helps regulate the speed of the motor. Electronic Speed Control (ESC): Some brushless motors in power tools feature electronic speed control (ESC) systems. ESC adjusts the power input to the motor based on user input or load conditions, providing variable speed control and optimizing efficiency. Overcurrent Protection: The control system may include overcurrent protection mechanisms. These protect the motor from excessive current that could lead to overheating or damage. Overcurrent protection enhances the safety and longevity of the motor. Thermal Management: Advanced brushless motor control systems incorporate thermal management features. Temperature sensors monitor the motor's temperature, and the control system adjusts the operation to prevent overheating. This can involve reducing power or implementing cooling mechanisms. Closed-Loop Control: In some applications, brushless motors operate in a closed-loop control system. This means that the system continuously adjusts motor operation based on real-time feedback, enhancing precision and stability. Soft Start and Stop: The control system may include soft start and stop features to minimize stress on the motor and mechanical components during acceleration and deceleration. Soft start and stop contribute to smoother operation and reduce wear. The combination of Hall Effect sensors, microcontrollers or DSPs, and advanced control algorithms allows brushless motors in power tools to offer benefits such as higher efficiency, longer lifespan, and precise control over speed and torque. The electronic control system plays a pivotal role in optimizing the motor's performance while ensuring safety and reliability.
MoreDC brushless motors are known for their power efficiency, and their application in surveillance and photography motors further highlights their advantages in this regard. Here are key factors that contribute to the power efficiency of DC brushless motors in these applications: Brushless Design: DC brushless motors operate without brushes, which reduces friction and wear. The absence of physical brushes eliminates the need for continuous maintenance and contributes to a more efficient operation. Reduced Heat Generation: DC brushless motors generate less heat compared to brushed motors. Heat is a byproduct of electrical resistance and friction, and by minimizing these factors, brushless motors operate cooler, contributing to higher efficiency. Precise Control: DC brushless motors can be precisely controlled using electronic commutation. This allows for optimal power delivery to meet the specific demands of the application, minimizing energy wastage. Variable Speed Control: The ability to control the speed of DC brushless motors provides flexibility in adapting to different operational requirements. They can operate efficiently at various speeds, consuming only the necessary amount of power. High Torque-to-Inertia Ratio: DC brushless motors often have a high torque-to-inertia ratio, meaning they can provide significant torque for a given amount of inertia. This efficiency is beneficial in applications where rapid acceleration or deceleration is required. Efficient Feedback Systems: Many DC brushless motors are equipped with feedback systems, such as encoders or sensors, which provide real-time information about the motor's position and speed. This feedback allows for precise control, optimizing power usage. Regenerative Braking: Some DC brushless motor systems incorporate regenerative braking, where the motor acts as a generator during deceleration. The generated electrical energy is fed back into the system, improving overall energy efficiency. Customizable Performance: DC brushless motors can be customized to match specific performance requirements. This customization includes adjusting parameters such as voltage, current, and speed to optimize power efficiency for a particular application. Low Friction Bearings: The use of low-friction bearings in DC brushless motors helps reduce mechanical losses, contributing to overall energy efficiency. Advanced Motor Control Algorithms: Modern motor control algorithms, such as sensorless control and field-oriented control (FOC), enhance the efficiency of DC brushless motors by optimizing the magnetic field and current flow. Integration with Energy-Efficient Systems: DC brushless motors are often integrated into systems designed for energy efficiency. For example, they can be part of camera stabilization gimbals that optimize power usage while providing smooth movements. Compact and Lightweight Design: The compact and lightweight design of DC brushless motors reduces inertia and allows for efficient energy transfer, especially in applications where weight and space considerations are critical. Electronic Commutation: The electronic commutation process in DC brushless motors eliminates the need for physical commutators and brushes, reducing electrical losses and increasing overall efficiency. Advancements in Motor Technology: Ongoing advancements in motor technology, including the use of advanced materials and manufacturing processes, contribute to improved efficiency and performance.
MoreFor exclusive deals and latest offers, sign up by entering your email address below.